
Define the problem:
- Purpose: Create an alternative home design by repurposing shipping containers.
- Location: Your choice. Select a site within your home’s or school’s neighborhood, which you can photograph and measure.
- Target audience: Individuals or families interested in alternative housing solutions.
- Size limitations: Up to four containers, 40 feet x 8 feet each
- Materials to be used: Containers and recycled materials.
- Budget constraints: $30,000.00 including the cost of the shipping containers, which cost about $6,000 each (see WikiHow for how to buy a shipping container)
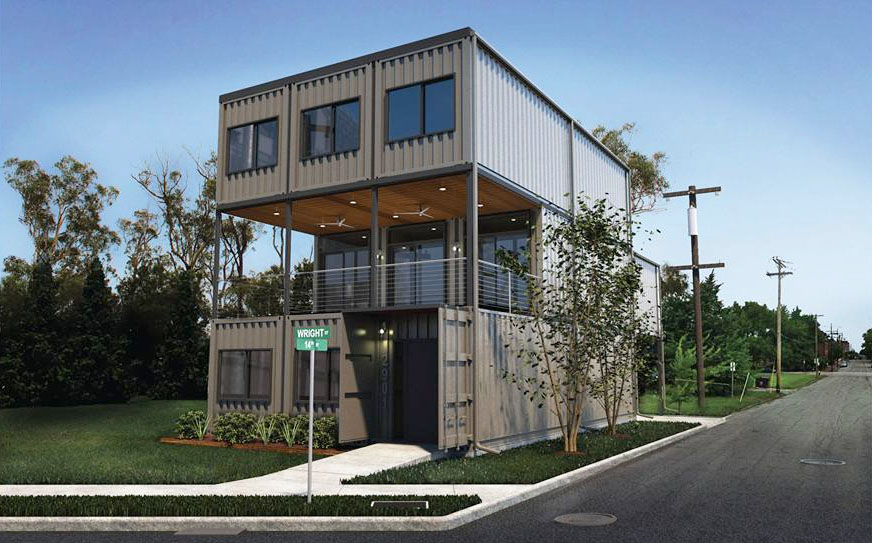
Advantages
- Strength and durability: Shipping containers are in many ways an ideal building material. They are designed to carry heavy loads and to be stacked in high columns. They are also designed to resist harsh environments, such as on ocean-going vessels or sprayed with road salt while transported on roads. Due to their high strength, containers are useful for secure storage.
- Modular: All shipping containers are made to standard measurements, and as such they provide modular elements that can be combined into larger structures. This simplifies design, planning and transport. As they are already designed to interlock for ease of mobility during transportation, structural construction is completed by simply emplacing them. Due to the containers' modular design, additional construction is as easy as stacking more containers. They can be stacked up to 12 high when empty.
- Labor: The welding and cutting of steel is considered to be specialized labor and can increase construction expenses, yet overall it is still lower than conventional construction. Unlike wood frame construction, attachments must be welded or drilled to the outer skin, which is more time consuming and requires different job site equipment.
- Transport: Pre-fabricated modules can also be easily transported by ship, truck or rail, because they already conform to standard shipping sizes.
- Availability: Used shipping containers are available across the globe.
- Expense: Many used containers are available at an amount that is low compared to a finished structure built by other labor-intensive means- such as bricks and mortar- which also require larger more expensive foundations. Construction involves very little labor and used shipping containers requiring only simple modification can be purchased from major transport companies for as little as US $1,200 each. Even when purchased brand new they are seldom more than US $6000.

Disadvantages
- Temperature: Steel conducts heat very well; containers used for human occupancy in an environment with extreme temperature variations will normally have to be better insulated than most brick, block or wood structures.
- Humidity: As noted above, single wall steel conducts heat. In temperate climates, moist interior air condenses against the steel, becoming clammy. Rust will form unless the steel is well sealed and insulated.
- Construction site: The size and weight of the containers will, in most cases, require them to be placed by a crane or forklift. Traditional brick, block and lumber construction materials can often be moved by hand, even to upper stories.
- Building permits: The use of steel for construction, while prevalent in industrial construction, is not widely used for residential structures. Obtaining building permits may be troublesome in some regions due to municipalities not having seen this application before.
- Treatment of timber floors: To meet Australian government quarantine requirements most container floors when manufactured are treated with insecticides containing copper (23-25%), chromium (38-45%) and arsenic (30-37%). Before human habitation, floors should be removed and safely disposed. Units with steel floors would be preferable, if available.
- Cargo spillages: A container can carry a wide variety of cargo during its working life. Spillages or contamination may have occurred on the inside surfaces and will have to be cleaned before habitation. Ideally all internal surfaces should be abrasive blasted to bare metal, and re-painted with a nontoxic paint system.
- Solvents: Solvents released from paint and sealants used in manufacture might be harmful.
- Damage While in service, containers are damaged by friction, handling collisions, and force of heavy loads overhead during ship transits. The companies will inspect containers and condemn them if cracked welds, twisted frames or pin holes are found, among other faults.

Container Home Blogs
A number of people have started personal blogs to document their progress as the build a container home and they can be a helpful account of all the decisions and tasks that were undertaken.
- Life in 320: A Container Home Story – Rachel and Alan’s story of building their container home in the high desert of California
- Cottonwood Meadow – Hannah and Kyle’s story of building their hybrid container home in the Sierra Nevada Mountain of California
- Brooklyn Farm Girl Upstate Adventure – Pamela and Matthew’s Upstate New York Container Home
- 40×28 – Ryan’s blog about building his container home in North Carolina. We also interviewed him here!
- Self-Containered – Terry’s blog about building a container home in Australia
- The 8747 House – Marti’s blog about building a container home in Missouri
- A Shipping Container House in Panama – Fred and Cynthia’s blog about building a container home in Panama
- Tin Can Cabin – Steve’s story of building a container home in Wisconsin
- Living in a Tin Can – Mary and Tom’s blog about their container home in Oklahoma
- Containerhouse – Paul’s blog about building and living in a container home in Australia
- Container Home With Storage – JustDIY’s blog about building a very minimalist container cabin with no bathroom
- Our Container Home – Curtis’s blog covers building and living in his container home in West Virginia
- My Shipping Container House – Todd’s blog about building his shipping container house
- Container House – John’s story of building a container home in South Carolina